The concentrate in the equalization tank contains suspended solids(SS) and also has high hardness. Both of them need to be removed by softening and TUF pretreatment.
The effluent from softening is treated by the material membrane. The material membrane selection depends on the appropriate molecular weight. According to the experimental result, the suitable molecular weight can be decided. In this case, part of the colloid and macromolecular organic matters can be selectively rejected by the chosen material membrane without rejecting hardness and salinity. This can provide a good environment for HPRO and MVR operation. Besides, the system is capable of 90-98 % recovery with lower operating pressure due to the material membrane characteristics. Additionally, a small amount of concentrate is further treated by desiccation.
The effluent from the material memtrane is concentrated by HPRO. Since the HPRO adopted the anti-pollution disc membrane module, it can highly concentrate the raw water, reducing the amount of evaporated water. Hence, the overall investment and operation cost can be saved.
The permeate quality from the material membrane is good for reducing the amount of anti-foam agent used in the MVR evaporation system. This can effectively eliminate the foaming phenomenon. In addition, the salt cannot be wrapped by the organic matter, which is beneficial for the stable and continuous evaporation crystallization. Besides, since MVR system can operate in acidic conditions with negative pressure and low temperature, the scaling and corrosion phenomenon can be prevented. Also, the foam is hard to generate, leading to the good evaporation condensate quality. The MVR permeate flows back to the membrane system for further treatment before discharge. The brine from MVR is treated by desiccation.
There are three kinds of sludge generated in this project, which need to be treated. They are the inorganic sludge from pretreatment, the brine sludge from evaporation crystallization and the sludge from desiccation.
The contract was signed in November, 2020. The equipment with 1000 m³/d treatment capacity was installed and accepted in April, 2020. The Jiarong Changshengqiao concentration ZLD project can be regarded as the WWT industry benchmark.
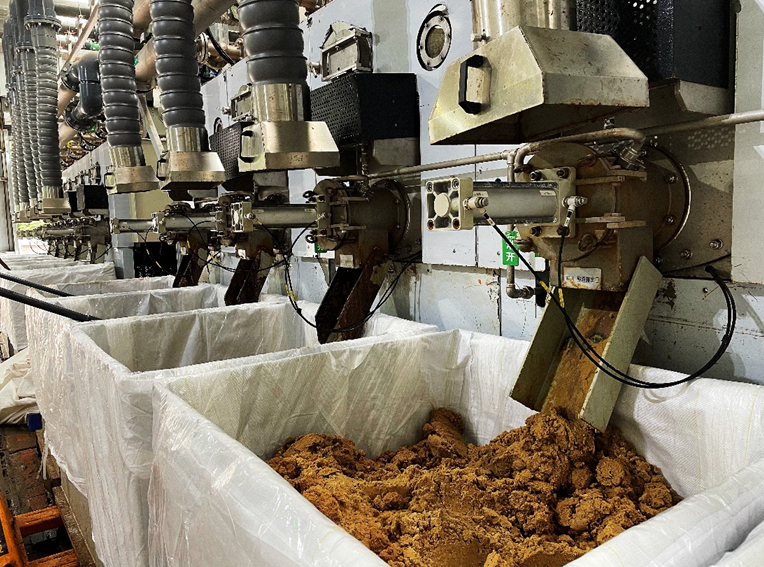
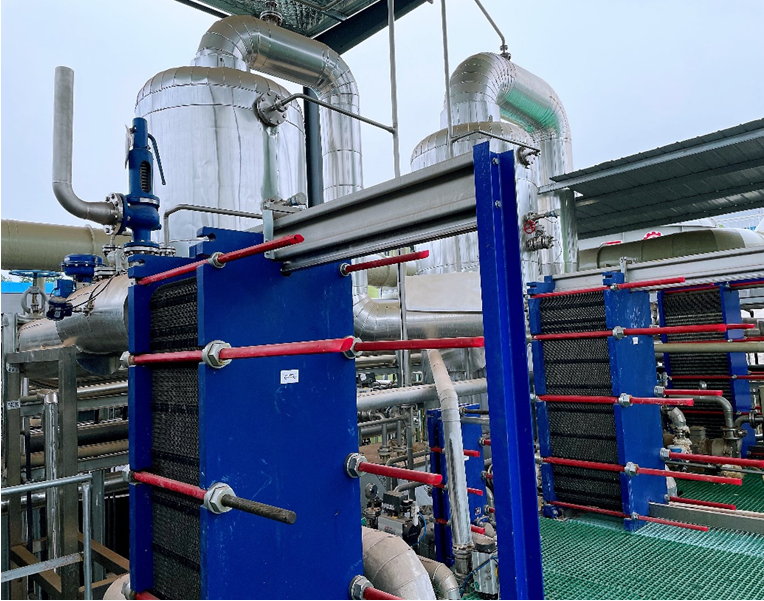